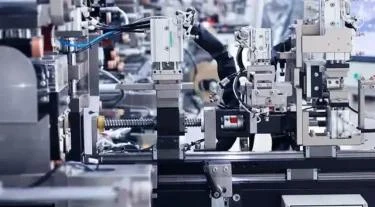
# Tape Production Process and Quality Control
## Introduction to Tape Manufacturing
Tape manufacturing is a complex process that involves multiple stages to ensure the final product meets industry standards and customer requirements. From raw material selection to final packaging, each step requires careful attention to detail and rigorous quality control measures.
## The Tape Production Process
### 1. Raw Material Preparation
The production process begins with the selection and preparation of raw materials. Different types of tapes require different base materials:
– Adhesive tapes: Typically use rubber, acrylic, or silicone-based adhesives
– Packaging tapes: Often use polypropylene or PVC films
– Electrical tapes: Usually made with vinyl or rubber materials
### 2. Coating Process
The coating stage is crucial in tape manufacturing:
– The adhesive is applied to the backing material using precision coating equipment
– Coating thickness is carefully controlled to ensure consistent performance
– Drying ovens remove solvents and cure the adhesive
### 3. Slitting and Rewinding
After coating and drying, the large rolls of tape are processed:
– Precision slitting machines cut the wide rolls into narrower widths
– Automated rewinding machines create smaller rolls for packaging
– Edge quality is monitored to prevent defects
### 4. Printing and Labeling (Optional)
For tapes requiring branding or identification:
– High-speed printing applies logos, text, or measurement markings
– UV curing ensures printed information remains durable
– Color matching systems maintain brand consistency
## Quality Control in Tape Manufacturing
### 1. Raw Material Inspection
Quality control begins before production:
– All incoming materials are tested for consistency and purity
– Adhesive samples are evaluated for tack, peel, and shear properties
– Backing materials are checked for thickness uniformity
### 2. In-Process Quality Checks
During production, multiple checks ensure quality:
– Coating weight is measured at regular intervals
– Adhesion tests are performed on samples from the production line
– Visual inspections identify surface defects or contamination
### 3. Final Product Testing
Before shipping, finished tapes undergo rigorous testing:
– Peel adhesion tests measure sticking power
– Tensile strength tests evaluate durability
– Temperature resistance tests ensure performance in various environments
– Aging tests predict long-term performance
## Advanced Quality Control Technologies
Modern tape manufacturers employ sophisticated technologies:
– Automated vision systems detect microscopic defects
– Laser measurement devices ensure precise thickness control
– Computerized data collection tracks quality metrics throughout production
– Statistical process control identifies trends and prevents defects
## Environmental Considerations
Responsible tape manufacturers implement:
– Waste reduction programs
– Energy-efficient production methods
– Recycling initiatives for production scraps
– Development of eco-friendly adhesive formulations
## Conclusion
The tape manufacturing process combines precision engineering with rigorous quality control to produce reliable products for countless applications. By maintaining strict standards at every production stage, manufacturers ensure their tapes perform as expected in industrial, commercial, and consumer settings. Continuous improvement in both production techniques and quality control methods helps the industry meet evolving customer needs while maintaining high standards of performance and reliability.
Keyword: tape manufacturing