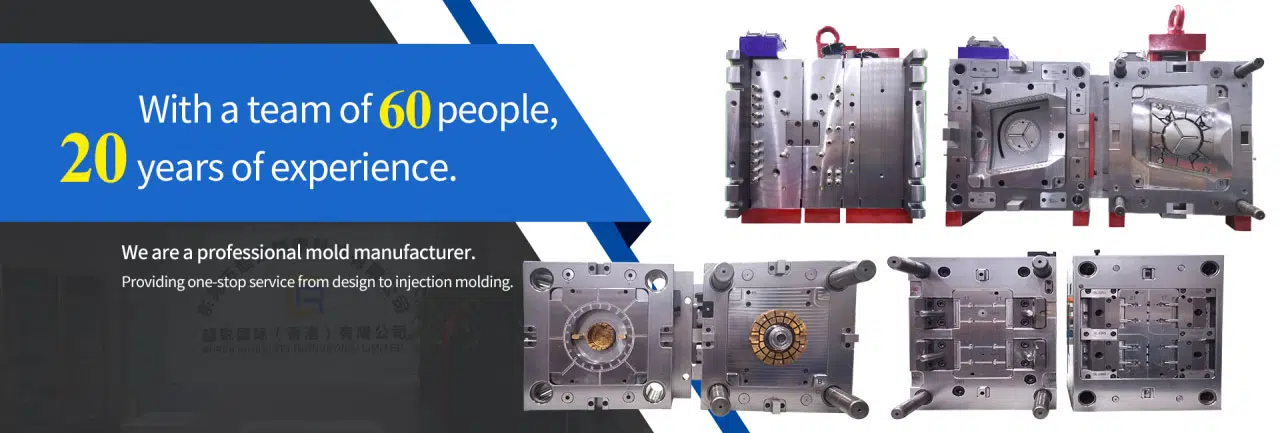
,文章长度在2000字左右
html
Low-Volume Manufacturing: Cost-Effective Solutions for Small Batch Production
In today’s fast-paced manufacturing landscape, businesses often face the challenge of producing small quantities of high-quality products without incurring excessive costs. Low-volume manufacturing has emerged as a game-changing solution, offering flexibility, efficiency, and cost-effectiveness for small batch production. This article explores the benefits, methods, and best practices of low-volume manufacturing.
What is Low-Volume Manufacturing?
Low-volume manufacturing refers to the production of limited quantities of parts or products, typically ranging from 10 to 10,000 units. Unlike mass production which focuses on high quantities at low per-unit costs, low-volume manufacturing prioritizes flexibility, customization, and rapid turnaround times while maintaining quality standards.
This approach is particularly valuable for:
- Startups testing new product concepts
- Companies launching limited edition products
- Businesses requiring replacement parts for legacy systems
- Medical device manufacturers producing specialized equipment
Advantages of Low-Volume Production
1. Reduced Upfront Costs
Traditional manufacturing often requires significant investment in tooling and setup before production can begin. Low-volume methods minimize these initial expenses, making product development more accessible to smaller businesses.
2. Faster Time-to-Market
With streamlined processes and minimal setup requirements, low-volume manufacturing allows companies to bring products to market quickly, gaining a competitive edge.
3. Greater Flexibility
Small batch production enables manufacturers to make design changes between production runs without costly retooling, allowing for continuous product improvement.
4. Lower Inventory Costs
By producing only what’s needed, businesses can avoid the financial burden of maintaining large inventories of finished goods.
Popular Low-Volume Manufacturing Methods
1. CNC Machining
Computer Numerical Control (CNC) machining offers precision and repeatability for metal and plastic parts. Modern CNC machines can quickly switch between different part designs, making them ideal for small batch production.
2. 3D Printing/Additive Manufacturing
Additive manufacturing technologies have revolutionized low-volume production by eliminating the need for expensive molds. From prototyping to end-use parts, 3D printing provides unmatched design freedom.
3. Vacuum Casting
This process uses silicone molds to produce high-quality plastic parts in small quantities. It’s particularly useful for creating functional prototypes or small batches of consumer products.
4. Sheet Metal Fabrication
Keyword: Low-Volume Manufacturing
For metal components, sheet metal fabrication offers a cost-effective solution for low-volume production with quick turnaround times.
Cost-Saving Strategies for Small Batch Production
To maximize the benefits of low-volume manufacturing, consider these cost-saving approaches:
1. Design for Manufacturability (DFM)
Optimizing your product design for the chosen manufacturing method can significantly reduce production costs. Work closely with your manufacturing partner during the design phase.
2. Material Selection
Choosing readily available materials rather than specialty options can lower costs without compromising quality.
3. Standardized Components
Where possible, incorporate standard off-the-shelf parts into your design to avoid custom manufacturing costs.