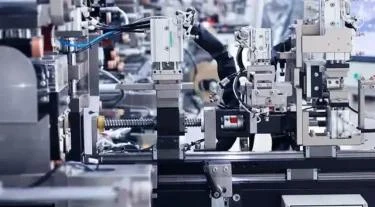
# Tape Production: Processes and Innovations in Manufacturing
## Introduction to Tape Manufacturing
Tape manufacturing is a complex process that involves multiple stages to produce high-quality adhesive products for various industries. From packaging to medical applications, tapes play a crucial role in modern society. The production of tape requires precision engineering, advanced materials science, and continuous innovation to meet evolving market demands.
## The Basic Tape Manufacturing Process
### 1. Raw Material Preparation
The tape manufacturing process begins with the preparation of raw materials. The primary components typically include:
– Backing materials (such as plastic films, paper, or cloth)
– Adhesive compounds (rubber-based, acrylic, or silicone)
– Release liners (for pressure-sensitive tapes)
– Additives and fillers for specific properties
### 2. Coating Process
The coating stage is where the adhesive is applied to the backing material. There are several coating methods used in tape production:
– Direct coating: The adhesive is applied directly onto the backing material
– Transfer coating: The adhesive is first applied to a release liner and then transferred to the backing
– Hot melt coating: The adhesive is applied in molten form and then cooled
### 3. Drying and Curing
After coating, the tape goes through drying ovens or curing chambers to remove solvents and achieve the desired adhesive properties. The temperature and duration of this process are carefully controlled to ensure optimal performance.
### 4. Slitting and Rewinding
Once the adhesive is properly cured, the large rolls of coated material are slit into narrower widths according to customer specifications. Precision slitting equipment ensures clean edges and consistent width throughout the roll.
## Innovations in Tape Manufacturing
### Advanced Adhesive Technologies
Recent innovations in tape production include:
– Environmentally friendly adhesives with reduced VOC emissions
– High-performance adhesives for extreme temperatures
– Reusable and repositionable adhesive systems
– Bio-based adhesives from renewable resources
### Smart Tape Solutions
The industry is seeing the development of intelligent tapes with special capabilities:
– Conductive tapes for electronic applications
– Temperature-sensitive color-changing tapes
– Self-healing adhesive systems
– Tapes with embedded sensors for structural monitoring
### Automation and Industry 4.0
Modern tape manufacturing facilities are incorporating:
– Automated quality control systems with machine vision
– Predictive maintenance using IoT sensors
– AI-driven process optimization
– Robotics for material handling and packaging
## Quality Control in Tape Production
Maintaining consistent quality is essential in tape manufacturing. Key quality control measures include:
– Adhesion strength testing
– Tensile strength measurements
– Thickness uniformity checks
– Visual inspection for defects
– Aging and environmental resistance testing
## Environmental Considerations
The tape manufacturing industry is increasingly focused on sustainability:
– Recycling programs for production waste
– Energy-efficient drying systems
– Water-based adhesive formulations
– Biodegradable backing materials
– Reduced packaging waste initiatives
## Future Trends in Tape Manufacturing
Looking ahead, the tape production industry is expected to see:
– Further development of sustainable materials
– Increased customization capabilities
– Integration with digital printing technologies
– Expansion into new industrial applications
– Continued improvement in performance characteristics
The tape manufacturing sector continues to evolve, driven by technological advancements and changing market needs. From traditional pressure-sensitive tapes to cutting-edge smart adhesive solutions, the industry demonstrates remarkable innovation while maintaining rigorous quality standards. As environmental concerns grow and new applications emerge, tape producers are well-positioned to meet these challenges with creative solutions and efficient manufacturing processes.
Keyword: tape manufacturing