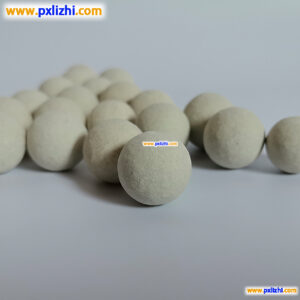
# Ceramic Ball Applications in Industrial Processes
## Introduction to Ceramic Balls
Ceramic balls are highly versatile components used across various industrial applications. Their unique properties, such as high wear resistance, thermal stability, and chemical inertness, make them indispensable in many processes. From grinding media to precision bearings, ceramic balls play a crucial role in enhancing efficiency and durability in industrial settings.
## Key Properties of Ceramic Balls
Before diving into applications, it’s essential to understand why ceramic balls are preferred in industrial processes:
– High hardness and wear resistance
– Excellent thermal stability
– Corrosion resistance
– Low density compared to metal alternatives
– Electrical insulation properties
## Major Industrial Applications
### 1. Grinding and Milling
Ceramic balls serve as excellent grinding media in ball mills, especially for:
– Mineral processing
– Paint and pigment production
– Pharmaceutical manufacturing
– Food processing
Their hardness ensures efficient particle size reduction while minimizing contamination.
### 2. Bearing Systems
Advanced ceramic balls are revolutionizing bearing technology in:
– High-speed machine tools
– Aerospace applications
– Medical equipment
– Automotive components
They offer superior performance in extreme conditions where traditional steel bearings would fail.
### 3. Valve Components
In fluid control systems, ceramic balls provide:
Keyword: ceramic ball
– Exceptional wear resistance in abrasive media
– Corrosion resistance in chemical processing
– Long service life in high-pressure applications
### 4. Catalysis and Chemical Processing
Ceramic balls serve as:
– Catalyst supports in petrochemical industries
– Inert packing materials in distillation columns
– Media for heat exchange systems
## Specialized Applications
### High-Temperature Environments
Ceramic balls excel in applications requiring thermal stability, such as:
– Furnace components
– Thermal barrier systems
– High-temperature bearings
### Electrical Insulation
Their non-conductive properties make ceramic balls ideal for:
– Electrical switchgear
– Insulating components in power transmission
– Electronic device manufacturing
## Advantages Over Metal Alternatives
When compared to traditional metal balls, ceramic balls offer:
– Longer service life
– Reduced maintenance requirements
– Energy savings due to lower density
– Better performance in corrosive environments
– Higher precision in critical applications
## Future Trends in Ceramic Ball Applications
The industrial use of ceramic balls continues to expand with:
– Development of advanced ceramic composites
– Increased adoption in renewable energy systems
– Growing demand in semiconductor manufacturing
– Innovations in medical implant technologies
## Conclusion
From grinding operations to precision machinery, ceramic balls have become essential components in modern industrial processes. Their unique combination of properties continues to drive innovation across multiple sectors, offering solutions where traditional materials fall short. As material science advances, we can expect even broader applications and improved performance from these remarkable spherical components.