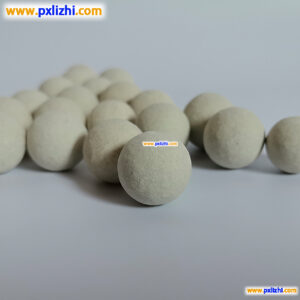
Keyword: ceramic ball
# Ceramic Ball Manufacturing Process
## Introduction to Ceramic Balls
Ceramic balls are precision-engineered components used in various industrial applications, including bearings, valves, and grinding media. Their exceptional hardness, wear resistance, and thermal stability make them superior to traditional metal balls in many demanding environments.
## Raw Material Selection
The manufacturing process begins with the careful selection of raw materials:
– Alumina (Al2O3)
– Zirconia (ZrO2)
– Silicon nitride (Si3N4)
– Silicon carbide (SiC)
The choice of material depends on the intended application and required properties such as hardness, toughness, and chemical resistance.
## Powder Preparation
The ceramic powder undergoes several preparation steps:
1. Milling to achieve uniform particle size
2. Mixing with binders and additives
3. Homogenization to ensure consistent composition
## Forming Process
Several methods are used to form ceramic balls:
### Dry Pressing
Powder is compressed in a die under high pressure to form green balls.
### Isostatic Pressing
Uniform pressure is applied from all directions to create more homogeneous green bodies.
### Injection Molding
Ceramic powder mixed with thermoplastic binder is injected into molds.
## Sintering
The formed green balls undergo sintering at high temperatures (typically 1400-1800°C) to achieve:
– Densification
– Strength development
– Final dimensional stability
## Grinding and Lapping
After sintering, the balls go through precision finishing processes:
1. Rough grinding to achieve spherical shape
2. Fine grinding for dimensional accuracy
3. Lapping for surface finish improvement
## Quality Control
Each ceramic ball undergoes rigorous testing:
– Dimensional accuracy (±0.1 μm)
– Surface roughness (Ra < 0.01 μm)
– Hardness testing (typically > 1500 HV)
– Roundness verification
## Applications of Ceramic Balls
Finished ceramic balls find use in:
– High-performance bearings
– Chemical pumps and valves
– Aerospace components
– Medical devices
– Semiconductor manufacturing equipment
## Conclusion
The ceramic ball manufacturing process combines advanced material science with precision engineering to produce components that meet the most demanding industrial requirements. Continuous improvements in manufacturing techniques ensure these products maintain their position as critical components in high-tech applications.