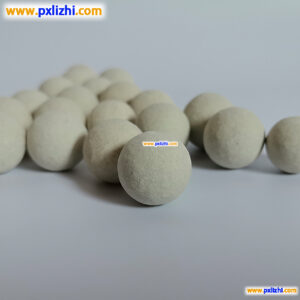
# Ceramic Ball Manufacturing Process and Applications
## Introduction to Ceramic Balls
Ceramic balls are precision-engineered spherical components made from various ceramic materials. These balls offer exceptional properties that make them suitable for a wide range of industrial applications. Their unique characteristics include high hardness, wear resistance, corrosion resistance, and thermal stability.
## The Manufacturing Process of Ceramic Balls
### 1. Raw Material Selection
The production of ceramic balls begins with the careful selection of raw materials. Common materials used include:
– Alumina (Al2O3)
– Zirconia (ZrO2)
– Silicon nitride (Si3N4)
– Silicon carbide (SiC)
### 2. Powder Preparation
The selected ceramic powder is mixed with binders and other additives to create a homogeneous mixture. This step is crucial for ensuring consistent properties throughout the final product.
### 3. Forming Process
There are several methods for forming ceramic balls:
– Dry pressing
– Isostatic pressing
– Injection molding
– Extrusion and spheronization
### 4. Sintering
The formed balls undergo a high-temperature sintering process, typically between 1400°C to 1800°C, depending on the material. This step densifies the ceramic and gives it its final mechanical properties.
### 5. Grinding and Polishing
After sintering, the balls go through precision grinding and polishing to achieve:
– Tight dimensional tolerances
– Excellent surface finish
– High sphericity
### 6. Quality Control
Each ceramic ball undergoes rigorous quality checks, including:
– Dimensional inspection
– Surface quality assessment
– Mechanical property testing
– Roundness measurement
## Applications of Ceramic Balls
### Bearings
Ceramic balls are widely used in high-performance bearings due to their:
– Low density
– High stiffness
– Corrosion resistance
– Ability to operate without lubrication
### Valves and Pumps
In fluid handling systems, ceramic balls provide:
– Excellent wear resistance
– Chemical inertness
– Long service life
### Grinding Media
Ceramic balls serve as grinding media in:
– Paint and pigment industries
– Pharmaceutical production
– Food processing
### Aerospace and Defense
Special applications include:
– Gyroscopes
– Guidance systems
– High-temperature components
## Advantages of Ceramic Balls Over Metal Balls
Property | Ceramic Balls | Metal Balls
Density | Lower | Higher
Hardness | Higher | Lower
Corrosion Resistance | Excellent | Variable
Thermal Stability | Superior | Limited
Electrical Conductivity | Insulating | Conductive
## Future Trends in Ceramic Ball Technology
Keyword: ceramic ball
The ceramic ball industry continues to evolve with:
– Development of new ceramic compositions
– Improved manufacturing techniques
– Nanotechnology applications
– Enhanced quality control methods
As industries demand higher performance and reliability, ceramic balls are becoming increasingly important components in modern engineering applications.