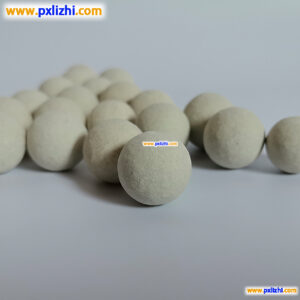
# Ceramic Ball Manufacturing Process and Applications
## Introduction to Ceramic Balls
Ceramic balls are precision-engineered spherical components made from various ceramic materials. These balls offer exceptional properties that make them suitable for a wide range of industrial applications. Their manufacturing process requires careful attention to detail to achieve the desired characteristics.
## The Manufacturing Process of Ceramic Balls
### 1. Raw Material Selection
The process begins with selecting high-quality ceramic materials such as alumina (Al2O3), zirconia (ZrO2), silicon nitride (Si3N4), or silicon carbide (SiC). The choice depends on the intended application and required properties.
### 2. Powder Preparation
The selected ceramic material is ground into fine powder and mixed with binders and additives to improve formability. This mixture is carefully controlled to ensure uniform composition.
### 3. Forming Process
There are several methods for forming ceramic balls:
– Dry pressing: Powder is compressed in spherical molds
– Isostatic pressing: Uniform pressure is applied from all directions
– Injection molding: Ceramic powder is mixed with plasticizers and injected into molds
### 4. Green Machining
After forming, the “green” (unfired) balls may undergo machining to achieve precise dimensions before firing.
### 5. Sintering
The formed balls are fired in high-temperature kilns (typically 1400-1700°C) to achieve full density and strength. This process causes the ceramic particles to bond together.
### 6. Precision Grinding and Lapping
After sintering, the balls undergo precision grinding and lapping to achieve:
– Tight dimensional tolerances (often within microns)
– Excellent sphericity
– Superior surface finish
### 7. Quality Control
Each ceramic ball undergoes rigorous inspection for:
– Diameter accuracy
– Roundness
– Surface quality
– Mechanical properties
## Applications of Ceramic Balls
### 1. Bearings
Ceramic balls are widely used in high-performance bearings for:
– Aerospace applications
– Medical equipment
– High-speed machinery
– Corrosive environments
### 2. Valves and Pumps
Their chemical resistance makes them ideal for:
– Chemical processing equipment
– Oil and gas applications
– Water treatment systems
### 3. Grinding Media
Ceramic balls serve as excellent grinding media for:
– Paint and pigment production
– Pharmaceutical manufacturing
– Food processing
### 4. Automotive Components
Used in various automotive applications including:
– Fuel injection systems
– Turbochargers
– High-performance engines
### 5. Electronics
Their electrical insulation properties make them suitable for:
Keyword: ceramic ball
– Electronic components
– Semiconductor manufacturing
– Insulating applications
## Advantages of Ceramic Balls
Ceramic balls offer numerous benefits compared to metal alternatives:
– High hardness and wear resistance
– Excellent corrosion resistance
– Lightweight (about 40-50% lighter than steel)
– High temperature stability
– Electrical insulation properties
– Non-magnetic characteristics
– Long service life
## Conclusion
The manufacturing of ceramic balls is a precise and technical process that results in components with exceptional properties. Their diverse applications across multiple industries demonstrate their versatility and performance advantages. As technology advances, we can expect to see even more innovative uses for these remarkable ceramic components in demanding environments.