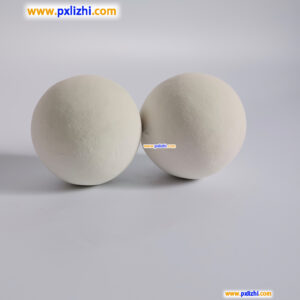
# Inert Ceramic Ball Applications in Industrial Processes
## Introduction to Inert Ceramic Balls
Inert ceramic balls are widely used in various industrial processes due to their excellent chemical stability, high temperature resistance, and mechanical strength. These spherical ceramic materials serve as essential components in numerous applications, providing support, distribution, and protection in harsh industrial environments.
## Key Properties of Inert Ceramic Balls
The effectiveness of inert ceramic balls in industrial applications stems from their unique characteristics:
– High chemical inertness
– Exceptional thermal stability
– Superior mechanical strength
– Low water absorption
– Resistance to corrosion and abrasion
– Uniform size and shape
## Major Industrial Applications
### 1. Petrochemical Industry
Inert ceramic balls play a crucial role in petrochemical processing:
As catalyst supports in reactors, they help distribute gases and liquids evenly while protecting the catalyst from mechanical damage. Their thermal stability makes them ideal for high-temperature processes like catalytic reforming and hydrocracking.
### 2. Chemical Processing
Chemical manufacturers utilize inert ceramic balls for:
Distillation column packing, where they improve vapor-liquid contact and separation efficiency. They’re also used as tower packing in absorption and stripping columns, providing large surface areas for mass transfer while resisting chemical attack.
### 3. Environmental Protection
Inert ceramic balls contribute to environmental applications:
In flue gas treatment systems, they support catalysts for removing pollutants like NOx and SOx. Their thermal stability allows operation in high-temperature exhaust streams from industrial furnaces and power plants.
### 4. Refining Processes
Oil refineries employ inert ceramic balls for:
Protecting expensive catalysts in hydroprocessing units. They serve as guard beds to filter out contaminants and distribute feedstocks evenly across the catalyst bed, extending catalyst life and improving process efficiency.
## Selection Considerations
When choosing inert ceramic balls for industrial applications, consider:
– Operating temperature range
– Chemical environment
– Pressure conditions
– Required mechanical strength
– Size and shape specifications
Keyword: inert ceramic ball
– Thermal shock resistance
## Maintenance and Handling
Proper handling of inert ceramic balls ensures optimal performance and longevity. Regular inspection for cracks or wear, proper loading techniques to prevent breakage, and appropriate cleaning procedures are essential maintenance practices.
## Future Trends
The demand for inert ceramic balls continues to grow with advancements in industrial processes. Developments in ceramic formulations promise even higher temperature resistance and improved mechanical properties for more demanding applications.