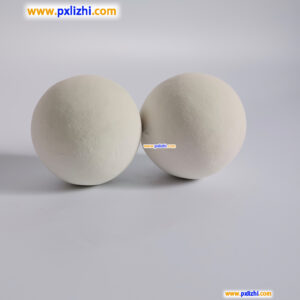
# Inert Ceramic Ball Applications in Industrial Processes
## Introduction to Inert Ceramic Balls
Inert ceramic balls are high-quality ceramic spheres made from chemically stable materials like alumina, zirconia, or silicon carbide. These balls are designed to withstand extreme temperatures, corrosive environments, and high-pressure conditions without reacting with the surrounding materials or altering the chemical composition of the process.
## Key Properties of Inert Ceramic Balls
The exceptional performance of inert ceramic balls in industrial applications stems from their unique properties:
– High thermal stability (up to 1800°C)
– Excellent chemical resistance
– Superior mechanical strength
– Low water absorption
– Resistance to thermal shock
– Uniform size and shape
## Major Industrial Applications
### 1. Petrochemical Industry
Inert ceramic balls play a crucial role in petrochemical processes:
– Used as catalyst supports in reactors
– Serve as tower packing in distillation columns
– Protect catalysts from fouling and coking
– Provide uniform gas/liquid distribution
### 2. Chemical Processing
Chemical manufacturers utilize inert ceramic balls for:
– Acid and alkali resistant environments
– High-temperature reaction vessels
– Corrosive media handling
– Filtration systems
Keyword: inert ceramic ball
### 3. Environmental Protection
These ceramic balls contribute to cleaner industrial operations:
– Used in scrubbers for flue gas treatment
– Support media for catalytic converters
– Wastewater treatment systems
– Air pollution control equipment
### 4. Refining Applications
In oil refineries, inert ceramic balls are essential for:
– Guard beds to protect catalysts
– Hydroprocessing units
– Reforming processes
– Desulfurization systems
## Benefits in Industrial Processes
The use of inert ceramic balls offers numerous advantages:
– Extended equipment lifespan due to reduced wear
– Improved process efficiency through better flow distribution
– Lower maintenance requirements
– Reduced downtime for catalyst replacement
– Cost savings through longer service intervals
## Selection Considerations
When choosing inert ceramic balls for industrial applications, consider:
– Chemical composition requirements
– Operating temperature range
– Pressure conditions
– Abrasion resistance needs
– Size and shape specifications
– Load-bearing capacity
## Future Trends
The demand for inert ceramic balls continues to grow as industries seek:
– Higher performance materials
– More environmentally friendly processes
– Increased energy efficiency
– Longer-lasting solutions
– Customized solutions for specific applications
As industrial processes become more demanding, inert ceramic balls will remain a critical component in ensuring reliable, efficient, and safe operations across multiple sectors.