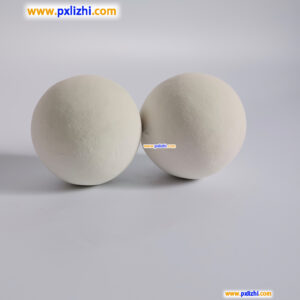
# Inert Ceramic Ball Applications in Industrial Processes
## Introduction to Inert Ceramic Balls
Inert ceramic balls are widely used in various industrial processes due to their excellent chemical stability, high mechanical strength, and thermal resistance. These small spherical ceramic pieces play crucial roles in numerous applications, particularly in petrochemical, chemical, and environmental industries.
## Key Properties of Inert Ceramic Balls
Before exploring their applications, it’s important to understand why inert ceramic balls are so valuable:
– Chemical inertness: They resist reactions with most chemicals
– High temperature resistance: Can withstand extreme heat conditions
– Mechanical strength: Durable under pressure and impact
– Thermal stability: Maintain properties across wide temperature ranges
– Low water absorption: Ideal for moisture-sensitive processes
## Major Industrial Applications
### 1. Catalyst Support in Petrochemical Industry
Inert ceramic balls serve as excellent catalyst supports in petroleum refining processes:
– Protecting catalysts from mechanical damage
– Distributing gas or liquid flow evenly
– Preventing catalyst bed compaction
– Used in hydrocracking, reforming, and isomerization units
### 2. Packing Material in Chemical Towers
Chemical processing towers utilize inert ceramic balls for:
– Distillation column packing
– Absorption tower media
– Mass transfer enhancement
– Creating uniform vapor/liquid distribution
### 3. Gas Treatment Systems
Environmental applications include:
– Flue gas desulfurization
– Waste gas purification
– Removing impurities from industrial emissions
– Acting as support media for scrubber systems
### 4. Heat Exchange Applications
Their thermal properties make them suitable for:
– Regenerative heat exchangers
– Thermal storage systems
– High-temperature heat transfer media
– Industrial furnace applications
## Selection Considerations
When choosing inert ceramic balls for industrial processes, consider:
– Size and diameter requirements
– Specific chemical resistance needs
– Operating temperature range
– Pressure conditions
– Flow characteristics
– Long-term stability requirements
## Maintenance and Handling
Proper care ensures optimal performance:
– Regular inspection for cracks or wear
– Proper cleaning procedures
Keyword: inert ceramic ball
– Correct storage conditions
– Appropriate loading techniques
– Monitoring for performance degradation
## Future Trends
The market for inert ceramic balls continues to grow with:
– Development of advanced ceramic materials
– Increased environmental regulations
– Expansion of petrochemical industries
– New applications in emerging technologies
– Improved manufacturing processes
Inert ceramic balls remain indispensable components in modern industrial processes, offering reliable performance in challenging environments across multiple sectors. Their versatility and durability ensure they will continue to play a vital role in industrial applications for years to come.