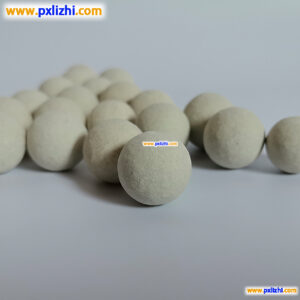
# Ceramic Ball Manufacturing Process and Applications
## Introduction to Ceramic Balls
Ceramic balls are highly specialized spherical components made from advanced ceramic materials. These precision-engineered spheres offer exceptional properties that make them valuable across various industries. Their unique characteristics stem from the manufacturing process and the ceramic materials used in their production.
## The Manufacturing Process of Ceramic Balls
### 1. Raw Material Selection
The production of ceramic balls begins with the careful selection of raw materials. Common ceramic materials used include:
– Alumina (Al2O3)
– Zirconia (ZrO2)
– Silicon nitride (Si3N4)
– Silicon carbide (SiC)
The choice of material depends on the intended application and required properties such as hardness, wear resistance, or thermal stability.
### 2. Powder Preparation
The selected ceramic powder undergoes several preparation steps:
– Milling to achieve uniform particle size
– Mixing with binders and additives
– Homogenization to ensure consistency
### 3. Forming Process
Several methods are used to form ceramic balls:
– Isostatic pressing: Applies uniform pressure from all directions
– Extrusion: Forces material through a die to form spherical shapes
– Slip casting: Uses liquid ceramic slurry in spherical molds
### 4. Sintering
The formed balls undergo high-temperature sintering (typically 1400-1700°C) to:
– Remove organic binders
– Densify the ceramic structure
– Achieve final mechanical properties
### 5. Precision Grinding and Polishing
Keyword: ceramic ball
After sintering, the balls undergo precision finishing:
– Diamond grinding to achieve exact dimensions
– Lapping for surface refinement
– Polishing to reach required surface finish
### 6. Quality Control
Each ceramic ball undergoes rigorous testing for:
– Dimensional accuracy
– Surface quality
– Mechanical properties
– Roundness and sphericity
## Applications of Ceramic Balls
### 1. Bearings
Ceramic balls are widely used in high-performance bearings due to their:
– Excellent wear resistance
– High stiffness
– Corrosion resistance
– Ability to operate without lubrication
### 2. Valves and Pumps
In fluid handling systems, ceramic balls provide:
– Superior chemical resistance
– Long service life
– Reduced maintenance requirements
### 3. Grinding Media
Ceramic balls serve as grinding media in:
– Paint and pigment production
– Pharmaceutical manufacturing
– Food processing
### 4. Aerospace and Defense
Specialized applications include:
– Guidance systems
– High-temperature components
– Wear-resistant parts
### 5. Medical Devices
Biocompatible ceramic balls are used in:
– Joint replacements
– Dental applications
– Surgical instruments
## Advantages of Ceramic Balls
Ceramic balls offer numerous benefits compared to metal alternatives:
– Higher hardness and wear resistance
– Lower density (reducing centrifugal forces)
– Better corrosion resistance
– Electrical insulation properties
– Ability to withstand extreme temperatures
## Future Trends in Ceramic Ball Technology
The ceramic ball industry continues to evolve with:
– Development of new ceramic composites
– Improved manufacturing techniques for higher precision
– Expansion into emerging applications like renewable energy
– Integration with smart technologies for condition monitoring
As material science advances, ceramic balls will likely find even broader applications across various high-tech industries.