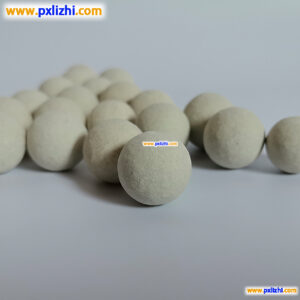
# Ceramic Ball Manufacturing Process and Applications
## Introduction to Ceramic Balls
Ceramic balls are highly engineered spherical components made from advanced ceramic materials. These precision balls offer exceptional properties that make them suitable for a wide range of demanding applications across various industries.
## Manufacturing Process of Ceramic Balls
### 1. Raw Material Selection
The production of ceramic balls begins with the careful selection of raw materials. Common materials include:
– Alumina (Al2O3)
– Zirconia (ZrO2)
– Silicon nitride (Si3N4)
– Silicon carbide (SiC)
### 2. Powder Preparation
The selected ceramic powder is processed to achieve:
– Uniform particle size distribution
– High purity levels
– Proper chemical composition
### 3. Forming Process
Several methods are used to form ceramic balls:
#### Isostatic Pressing
Cold isostatic pressing (CIP) applies uniform pressure from all directions to create green balls with consistent density.
#### Extrusion and Spheronization
This method involves extruding the ceramic paste and then rounding the pieces into spherical shapes.
#### Rolling Process
Pre-formed pellets are rolled between rotating plates to achieve spherical geometry.
### 4. Sintering
The formed balls undergo high-temperature sintering to:
– Achieve full density
– Develop the desired microstructure
– Obtain final mechanical properties
### 5. Precision Grinding and Lapping
After sintering, the balls go through precision finishing processes:
– Diamond grinding for size control
– Lapping for surface finish improvement
– Polishing for ultra-smooth surfaces
### 6. Quality Control
Each ceramic ball undergoes rigorous inspection for:
– Dimensional accuracy
– Surface quality
– Mechanical properties
– Chemical composition
## Applications of Ceramic Balls
### Bearings
Ceramic balls are widely used in high-performance bearings for:
– Aerospace applications
– Medical equipment
– High-speed machinery
– Corrosive environments
### Valves and Pumps
In fluid handling systems, ceramic balls provide:
– Excellent wear resistance
– Chemical inertness
– Long service life
### Grinding Media
Ceramic grinding balls are used in:
– Mineral processing
– Paint and pigment production
– Pharmaceutical manufacturing
### Other Applications
Additional uses include:
– Ball screws and linear guides
– Flow control devices
– Precision measurement instruments
– Decorative purposes
Keyword: ceramic ball
## Advantages of Ceramic Balls
Ceramic balls offer numerous benefits compared to metal alternatives:
– High hardness and wear resistance
– Excellent corrosion resistance
– Low density for reduced weight
– High temperature capability
– Electrical insulation properties
– Non-magnetic characteristics
## Conclusion
The manufacturing of ceramic balls requires precise control at every stage to achieve the desired properties. These advanced components continue to find new applications as technology advances, offering solutions where traditional materials fall short. With their unique combination of properties, ceramic balls play a critical role in modern engineering and industrial applications.