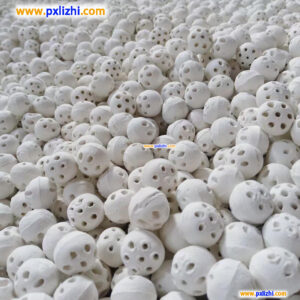
# Alumina Ceramic Ball Applications and Properties
## Introduction to Alumina Ceramic Balls
Alumina ceramic balls are high-performance ceramic spheres made from aluminum oxide (Al2O3). These balls exhibit exceptional mechanical, thermal, and chemical properties, making them suitable for various industrial applications. With alumina content typically ranging from 92% to 99.9%, these ceramic balls offer different levels of performance based on their composition.
## Key Properties of Alumina Ceramic Balls
### 1. High Hardness and Wear Resistance
Alumina ceramic balls rank 9 on the Mohs hardness scale, just below diamonds. This extreme hardness makes them highly resistant to wear and abrasion, even under continuous operation in harsh environments.
### 2. Excellent Thermal Stability
These ceramic balls can withstand temperatures up to 1600°C (2912°F) without significant degradation, maintaining their structural integrity and dimensional stability.
### 3. Chemical Inertness
Alumina ceramic balls are resistant to most acids, alkalis, and organic solvents, making them ideal for corrosive environments where metal balls would fail.
### 4. Electrical Insulation
With high dielectric strength and volume resistivity, alumina balls serve as excellent electrical insulators in various applications.
### 5. Low Density
Compared to steel balls, alumina ceramic balls are about 60% lighter, reducing energy consumption in rotating applications.
## Common Applications of Alumina Ceramic Balls
### 1. Grinding Media
In ball mills and attritors, alumina ceramic balls are widely used as grinding media for:
– Ceramic raw materials
– Minerals
– Paints and coatings
– Pharmaceuticals
– Food products
Keyword: alumina ceramic ball
### 2. Bearing Components
Due to their hardness and wear resistance, alumina balls are used in:
– Precision bearings for high-speed applications
– Corrosive environment bearings
– High-temperature bearings
### 3. Valve Components
Alumina ceramic balls serve as:
– Valve balls in chemical processing
– Check valve components
– Flow control elements
### 4. Catalyst Supports
In chemical reactors, alumina balls provide:
– High surface area for catalyst deposition
– Thermal stability for high-temperature reactions
– Chemical resistance to reaction media
### 5. Other Industrial Applications
– Pump components in abrasive slurry handling
– Wear-resistant liners
– Semiconductor manufacturing equipment
– Textile machinery guides
## Manufacturing Process
Alumina ceramic balls are produced through:
1. Powder preparation and mixing
2. Forming (isostatic pressing or extrusion)
3. High-temperature sintering (1500-1700°C)
4. Precision grinding and polishing
5. Quality inspection and sorting
## Selection Considerations
When choosing alumina ceramic balls, consider:
– Alumina content (92%, 95%, 99%, or 99.9%)
– Diameter tolerance
– Surface finish requirements
– Operating environment (temperature, chemicals, pressure)
– Load and stress conditions
## Advantages Over Metal Balls
Compared to traditional metal balls, alumina ceramic balls offer:
– Longer service life in abrasive environments
– Reduced maintenance costs
– Better performance in corrosive conditions
– Lower energy consumption due to reduced weight
– Non-magnetic and non-conductive properties
## Conclusion
Alumina ceramic balls represent a high-performance solution for demanding industrial applications where conventional materials fail. Their unique combination of properties makes them indispensable in modern manufacturing processes across various industries. As technology advances, we can expect to see even broader applications for these versatile ceramic components.