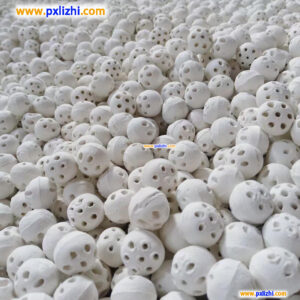
# Alumina Cerical Ball Applications and Properties
## Introduction to Alumina Ceramic Balls
Alumina ceramic balls are high-performance ceramic spheres made from aluminum oxide (Al2O3). These balls exhibit exceptional mechanical, thermal, and chemical properties, making them ideal for various industrial applications. With their excellent wear resistance and high-temperature stability, alumina ceramic balls have become indispensable components in many demanding environments.
## Key Properties of Alumina Ceramic Balls
### 1. High Hardness and Wear Resistance
Alumina ceramic balls boast a Mohs hardness of 9, second only to diamond. This exceptional hardness provides outstanding wear resistance, significantly outperforming steel balls in abrasive environments.
### 2. Excellent Thermal Stability
These ceramic balls can withstand temperatures up to 1600°C (2912°F) without significant degradation, making them suitable for high-temperature applications where metal balls would fail.
### 3. Chemical Inertness
Alumina ceramic balls are highly resistant to most acids, alkalis, and organic solvents, ensuring long-term performance in corrosive environments.
### 4. Low Density
With a density of approximately 3.6-3.9 g/cm³, alumina ceramic balls are about 50% lighter than steel balls, reducing energy consumption in rotating applications.
### 5. Electrical Insulation
These ceramic balls provide excellent electrical insulation properties, with high dielectric strength and low electrical conductivity.
## Common Applications of Alumina Ceramic Balls
### 1. Bearing Systems
Alumina ceramic balls are widely used in hybrid and full ceramic bearings for applications requiring high-speed operation, corrosion resistance, or non-magnetic properties.
### 2. Grinding Media
In the mining and pigment industries, alumina ceramic balls serve as grinding media in ball mills due to their wear resistance and contamination-free grinding.
### 3. Valve Components
The chemical inertness of alumina ceramic balls makes them ideal for use in valves handling corrosive fluids in chemical processing plants.
### 4. Semiconductor Manufacturing
In the electronics industry, these ceramic balls are used in wafer handling and processing equipment where contamination must be minimized.
### 5. Aerospace Applications
Alumina ceramic balls find use in aerospace components where lightweight, high-strength materials are required for extreme environments.
## Grades of Alumina Ceramic Balls
Keyword: alumina ceramic ball
Alumina ceramic balls are available in different purity grades:
– 92% Alumina: Good mechanical properties with moderate cost
– 95% Alumina: Improved wear resistance and strength
– 99% Alumina: Highest purity with superior properties
– Zirconia-toughened alumina: Enhanced fracture toughness
## Manufacturing Process
The production of alumina ceramic balls involves several key steps:
1. Powder preparation and mixing
2. Forming through isostatic pressing or extrusion
3. High-temperature sintering (1500-1700°C)
4. Precision grinding and polishing
5. Quality inspection and sorting
## Advantages Over Metal Balls
Compared to traditional metal balls, alumina ceramic balls offer:
– Longer service life in abrasive environments
– Reduced maintenance requirements
– Lower energy consumption due to lighter weight
– Better performance in corrosive conditions
– Non-magnetic and non-sparking properties
## Conclusion
Alumina ceramic balls represent a high-performance solution for demanding industrial applications. Their unique combination of properties makes them superior to traditional materials in many scenarios. As technology advances, we can expect to see even broader adoption of these versatile ceramic components across various industries.