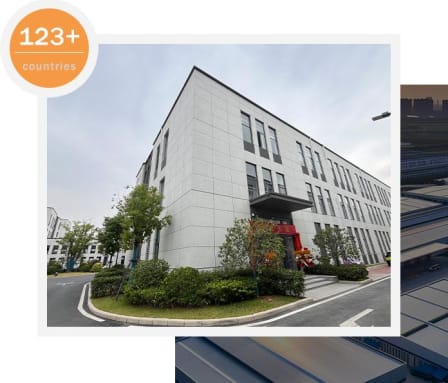
# PDC Bit Cutter Technology in Drilling Applications
Keyword: pdc bit cutter
## Introduction to PDC Bit Cutters
Polycrystalline Diamond Compact (PDC) bit cutters have revolutionized the drilling industry with their exceptional durability and cutting efficiency. These advanced cutting tools consist of a synthetic diamond layer bonded to a tungsten carbide substrate, offering superior performance in various drilling applications.
## How PDC Cutters Work
The unique design of PDC cutters allows them to shear rock formations rather than crush them like traditional roller cone bits. The diamond table provides extreme hardness while the carbide substrate offers excellent impact resistance. This combination enables:
– Faster penetration rates
– Longer bit life
– Improved drilling efficiency
– Reduced vibration and torque
## Advantages Over Conventional Bits
PDC cutters offer several significant benefits compared to conventional drill bits:
Enhanced Durability
The diamond surface of PDC cutters is extremely wear-resistant, allowing them to maintain sharp cutting edges throughout extended drilling operations.
Improved Rate of Penetration
PDC bits can achieve 2-4 times the penetration rates of conventional roller cone bits in suitable formations.
Cost Efficiency
While initial costs may be higher, the extended lifespan and improved performance of PDC bits often result in lower overall drilling costs.
## Applications in Different Formations
PDC cutters perform exceptionally well in:
– Soft to medium-hard formations
– Homogeneous rock structures
– Non-abrasive environments
– Directional drilling applications
However, their performance may be less optimal in extremely hard, abrasive, or fractured formations where impact damage can occur.
## Technological Advancements
Recent developments in PDC cutter technology include:
Thermally Stable Designs
New heat-resistant formulations allow PDC cutters to maintain performance at higher temperatures encountered in deep drilling applications.
Improved Bonding Techniques
Advanced manufacturing processes have enhanced the bond strength between the diamond layer and carbide substrate.
Customized Cutter Geometries
Specialized shapes and arrangements optimize performance for specific formation types and drilling conditions.
## Maintenance and Optimization
To maximize the benefits of PDC cutter technology, operators should:
– Match bit design to formation characteristics
– Optimize drilling parameters (weight on bit, RPM)
– Monitor cutter wear patterns
– Implement proper bit cleaning procedures
## Future Outlook
As drilling operations push into more challenging environments, PDC cutter technology continues to evolve. Research focuses on:
– Enhanced thermal stability
– Improved impact resistance
– Advanced cutter shapes and arrangements
– Integration with smart drilling systems
The ongoing development of PDC cutter technology promises to further improve drilling efficiency and reduce operational costs across the industry.