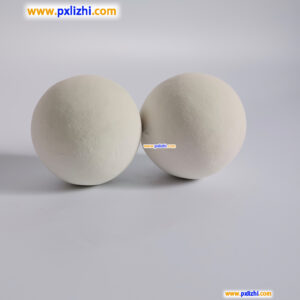
# Inert Ceramic Balls for Industrial Applications
## Introduction to Inert Ceramic Balls
Inert ceramic balls are widely used in various industrial applications due to their excellent chemical stability, high mechanical strength, and thermal resistance. These small spherical ceramic components play a crucial role in many chemical and petrochemical processes, serving as catalyst supports, tower packing, and grinding media.
## Key Properties of Inert Ceramic Balls
The effectiveness of inert ceramic balls in industrial settings stems from their unique combination of properties:
– High temperature resistance (up to 1600°C)
– Excellent chemical inertness
– Superior mechanical strength
– Low water absorption
– Good thermal shock resistance
– Resistance to corrosion and abrasion
## Manufacturing Process
Inert ceramic balls are typically manufactured through a precise process that includes:
1. Raw material selection (usually high-purity alumina or zirconia)
2. Mixing and grinding
3. Forming (through extrusion or pressing)
4. High-temperature sintering
5. Quality inspection and grading
## Common Industrial Applications
### Catalyst Support in Chemical Reactors
Inert ceramic balls serve as excellent catalyst supports in fixed-bed reactors, providing a stable surface for catalytic materials while ensuring proper gas or liquid distribution.
### Tower Packing in Distillation Columns
These ceramic balls are used as random packing in distillation and absorption towers, improving mass transfer efficiency while withstanding harsh chemical environments.
### Grinding Media
Due to their hardness and wear resistance, inert ceramic balls are ideal grinding media for ball mills in mineral processing and paint manufacturing.
### Heat Exchange Systems
In high-temperature heat exchange applications, ceramic balls help maintain structural integrity while facilitating efficient heat transfer.
## Advantages Over Alternative Materials
Compared to metal or plastic alternatives, inert ceramic balls offer:
– Longer service life in corrosive environments
– Better performance at extreme temperatures
– Lower maintenance requirements
– Reduced contamination risk in sensitive processes
– More consistent performance over time
## Selection Considerations
When choosing inert ceramic balls for industrial applications, consider:
– Chemical compatibility with process media
– Operating temperature range
– Required mechanical strength
– Size and density specifications
– Surface characteristics
– Cost-effectiveness for the specific application
## Maintenance and Handling
Proper handling of inert ceramic balls includes:
– Careful loading and unloading to prevent breakage
– Regular inspection for wear or damage
– Proper cleaning procedures when changing applications
– Appropriate storage conditions to prevent contamination
## Future Developments
Keyword: inert ceramic ball
The inert ceramic ball industry continues to evolve with:
– Development of new ceramic compositions
– Improved manufacturing techniques for higher precision
– Customized solutions for specific industrial needs
– Enhanced surface treatments for specialized applications
As industrial processes become more demanding, inert ceramic balls remain a reliable solution for numerous challenging applications across various sectors.