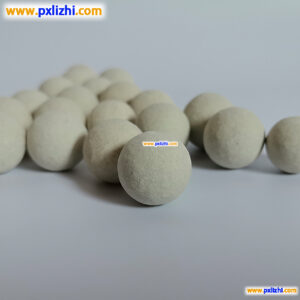
# Ceramic Ball Manufacturing Process and Applications
## Introduction to Ceramic Balls
Ceramic balls are precision spherical components made from various ceramic materials, offering exceptional properties such as high hardness, wear resistance, and chemical stability. These versatile components find applications across multiple industries, from bearings to medical devices.
## Manufacturing Process of Ceramic Balls
### 1. Material Selection
The manufacturing process begins with selecting appropriate ceramic materials based on the intended application. Common materials include:
– Alumina (Al2O3)
– Zirconia (ZrO2)
– Silicon nitride (Si3N4)
– Silicon carbide (SiC)
### 2. Powder Preparation
High-purity ceramic powders are carefully measured and mixed with binders and other additives to create a homogeneous mixture. This step ensures consistent material properties throughout the final product.
### 3. Forming Methods
Several forming techniques are employed in ceramic ball production:
– Dry pressing: Powder is compressed in spherical molds
– Isostatic pressing: Uniform pressure from all directions
– Injection molding: For complex shapes and high-volume production
– Extrusion and spheronization: For creating spherical shapes
### 4. Sintering
The formed balls undergo high-temperature sintering (typically 1400-1700°C) to achieve full density and desired mechanical properties. This critical step transforms the porous green body into a dense ceramic structure.
### 5. Precision Grinding and Lapping
After sintering, the balls undergo precision grinding and lapping to achieve:
– Tight dimensional tolerances (often within microns)
– Superior surface finish (Ra < 0.01 μm)
Keyword: ceramic ball
– Perfect sphericity (roundness < 0.1 μm)
### 6. Quality Control
Rigorous quality checks ensure each ceramic ball meets specifications:
– Dimensional verification
– Surface roughness measurement
– Hardness testing
– Visual inspection for defects
## Applications of Ceramic Balls
### Bearings and Mechanical Components
Ceramic balls are widely used in high-performance bearings for:
– Aerospace applications
– High-speed machine tools
– Medical equipment
– Semiconductor manufacturing
### Valve Components
Their chemical resistance makes ceramic balls ideal for:
– Chemical processing valves
– Oil and gas applications
– Water treatment systems
### Grinding Media
Ceramic grinding balls are used in:
– Paint and pigment production
– Pharmaceutical processing
– Food industry applications
### Other Specialized Uses
– Ballistic protection
– Precision measurement devices
– Decorative applications
– Spacecraft components
## Advantages of Ceramic Balls
The unique properties of ceramic balls offer several advantages:
– Exceptional hardness and wear resistance
– Corrosion resistance to chemicals and solvents
– High-temperature stability
– Electrical insulation properties
– Lightweight compared to metal alternatives
– Non-magnetic characteristics
## Future Trends in Ceramic Ball Technology
Emerging developments include:
– Nanostructured ceramic materials for enhanced properties
– Hybrid ceramic-metal composites
– Advanced coating technologies
– Additive manufacturing techniques for complex geometries
– Smart ceramic balls with embedded sensors
As manufacturing techniques continue to advance, ceramic balls are finding new applications across industries, pushing the boundaries of performance in demanding environments.