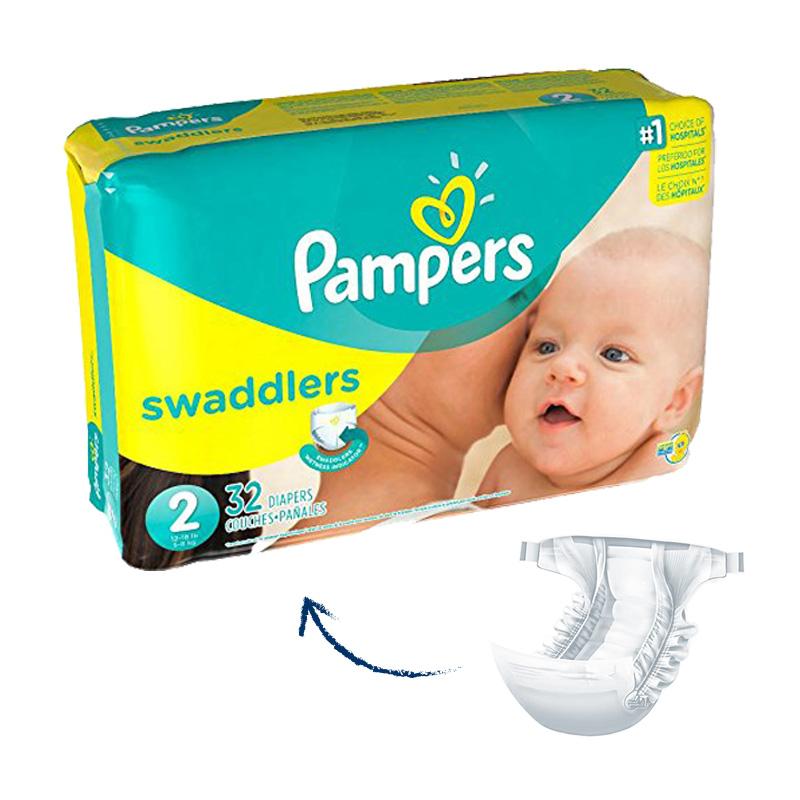
# Sustainable Pet Food Packaging Bags for Eco-Friendly Pet Care
## The Importance of Eco-Friendly Pet Food Packaging
As pet owners become increasingly conscious of their environmental impact, the demand for sustainable pet food packaging bags has grown significantly. Traditional plastic packaging contributes to pollution and takes hundreds of years to decompose, making eco-friendly alternatives essential for responsible pet care.
## What Makes Pet Food Packaging Sustainable?
Sustainable pet food packaging bags typically feature:
– Biodegradable or compostable materials
– Recycled content
– Minimalist designs to reduce waste
– Reusable features
– Non-toxic inks and adhesives
## Popular Materials for Eco-Conscious Packaging
### 1. Plant-Based Plastics
These innovative materials derived from corn, sugarcane, or other plant sources offer similar functionality to traditional plastics but with much lower environmental impact.
### 2. Recycled Materials
Post-consumer recycled plastics and papers give new life to existing materials while reducing the need for virgin resources.
### 3. Paper-Based Solutions
Kraft paper and other paper-based packaging options provide excellent biodegradability when properly treated for food safety.
## Benefits of Switching to Sustainable Pet Food Bags
Choosing eco-friendly pet food packaging offers numerous advantages:
– Reduced carbon footprint
– Less waste in landfills
– Safer for pets and the environment
– Aligns with consumer values
– Potential cost savings through material efficiency
## How to Identify Truly Sustainable Options
When selecting pet food packaging bags, look for:
Keyword: pet food packaging bag
– Third-party certifications (e.g., BPI, FSC)
– Clear recycling instructions
– Transparent material sourcing
– Minimal layers and components
– Proper food-grade safety standards
## The Future of Pet Food Packaging
Innovations in sustainable packaging continue to emerge, including:
– Edible packaging materials
– Water-soluble films
– Mushroom-based packaging
– Advanced recycling technologies
– Smart packaging that extends freshness
## Making the Switch: Tips for Pet Owners
Transitioning to sustainable pet food packaging is easier than you might think:
– Start by choosing brands that prioritize eco-friendly packaging
– Properly clean and recycle packaging when possible
– Consider bulk purchases to reduce packaging waste
– Support companies investing in sustainable innovations
– Spread awareness among fellow pet owners
By choosing sustainable pet food packaging bags, we can provide excellent care for our pets while protecting the planet they call home too. Every small change contributes to a healthier environment for future generations of pets and their owners.