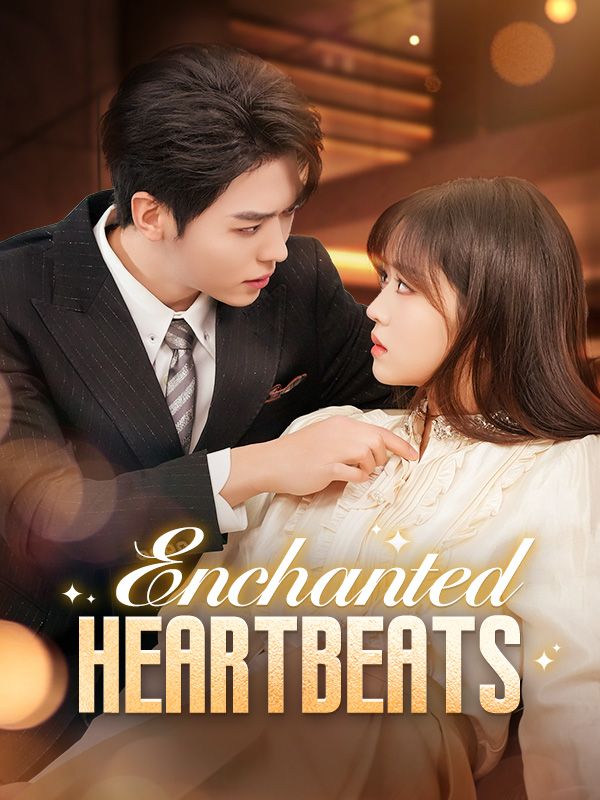
Watch Short Dramas Online for Free: The Ultimate Guide to Binge-Worthy Mini Series
Short dramas have taken the streaming world by storm, offering powerful storytelling in compact episodes. This guide explores how and where you can Watch Short Dramas Online for Free while diving into top platforms and genres worth your time.
Top Platforms for Short Drama Streaming
Leading platforms like YouTube, Viki, and TikTok host vast libraries of mini series across romance, thriller, and comedy genres. These sites offer user-friendly interfaces and personalized recommendations to enhance your viewing experience.
Why Short Dramas Are Growing in Popularity
With busy lifestyles, viewers appreciate condensed narratives that deliver emotional impact quickly. Short dramas often feature high-quality production, talented actors, and creative plots that rival traditional series.
How to Access Free Content Legally
Many platforms provide free ad-supported streaming, while others offer trial periods. Always use official sources to support creators and avoid piracy risks.
Curated Genres and Recommendations
From romantic comedies to suspenseful mysteries, discover hidden gems tailored to your preferences. We update our lists seasonally to include trending titles.
FAQ Section
Are these dramas really free to watch?
Yes, many platforms offer free access with ads or limited-time trials.
Do I need to create an account?
Some services require registration, but numerous options allow instant viewing without sign-up.
Can I download episodes for offline viewing?
Select platforms provide download options for premium users, but free access typically requires online streaming.
Start Your Binge-Watch Journey Today!
Explore our updated catalog of top-rated short dramas and discover your next obsession. Share your favorite finds with friends and join the community of mini-series enthusiasts!