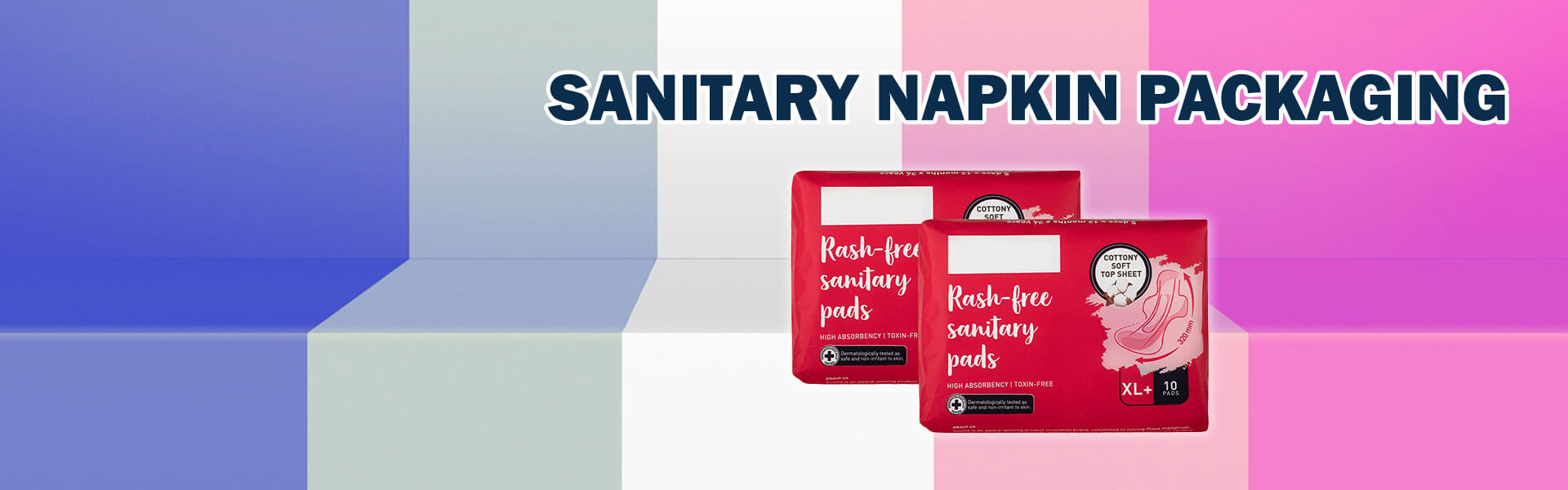
# Baby Diaper Packaging Design: Innovative and Functional Solutions
## The Importance of Effective Diaper Packaging
Baby diaper packaging design plays a crucial role in both product protection and consumer appeal. In today’s competitive market, manufacturers must balance functionality with aesthetics to create packaging that stands out on shelves while maintaining product integrity.
Modern parents seek convenience, sustainability, and clear information when choosing diaper products. The packaging serves as the first point of contact between the brand and potential customers, making its design a critical factor in purchasing decisions.
## Key Elements of Successful Diaper Packaging
### 1. Visual Appeal and Brand Recognition
Eye-catching designs with vibrant colors and clear branding help products stand out in crowded retail environments. Many brands use:
– Playful illustrations of babies or animals
– Color-coded systems for different sizes
– Clear product photography
– Recognizable logos and mascots
### 2. Functional Design Features
Practical considerations are equally important in diaper packaging:
– Resealable closures for maintaining freshness
– Easy-open features for quick access
– Ergonomic handles for comfortable carrying
– Tear strips for clean opening
– Moisture indicators (in some premium products)
## Sustainability in Diaper Packaging
Environmental concerns have led to significant innovations in diaper packaging materials and design:
– Biodegradable and compostable materials
– Reduced plastic content
– Minimalist designs using less material
– Recyclable components
– Soy-based inks for printing
Many brands now highlight their eco-friendly packaging as a key selling point to environmentally conscious parents.
## Information and Communication
Effective packaging communicates essential information clearly:
– Size and weight recommendations
– Absorbency levels
– Materials and ingredients
– Usage instructions
– Safety certifications
– Environmental claims (when applicable)
QR codes are increasingly used to provide additional digital content while keeping packaging clean and uncluttered.
## Future Trends in Diaper Packaging
The diaper packaging industry continues to evolve with several emerging trends:
– Smart packaging with NFC technology
– Interactive elements for parent engagement
– Customizable packaging options
– Ultra-thin but durable materials
Keyword: baby diaper packaging design
– Subscription-based packaging solutions
– Augmented reality experiences
As consumer preferences shift toward convenience and sustainability, diaper packaging design will continue to innovate to meet these demands while maintaining product quality and brand identity.